LWM – Laser Welding Monitoring
Monitoring your laser welding processes in real time.
Advantages
+ 100% traceability and transparency
The system is easy and intuitive to use and provides you with helpful data on your laser welding seam. The allocation to each component is done via communication with the system control/SPS. All data is stored and documented continuously, even during ongoing production. In combination with online backups, the LWM 4.0 thus enables 100 % traceability and transparency of your laser welding processes.
+ Intelligent adaptation of error detection
The introduction of new material batches into production can lead to systematic, erratic shifts in process signals. These values can be detected by the intelligent software package and the good part classification can be automatically adjusted. Due to this automatic adaptation, good parts are still classified as good parts and therefore no need for a new teach-in.
+ Detection of trends
During the mass production process, wear and tear of individual machining tools occurs. This can influence the joining process and thus the quality of the laser weld seam. The LWM 4.0 process monitoring system detects this systematic, continuous shift in signals and provides the user with early feedback via adjustable warning levels. Furthermore, these trends can be evaluated via individual statistics.
Techn7ical data | |||
---|---|---|---|
Solid state laser application: for IR / blue / green laser and CW or pulsed mode
Installation options: possible in welding optics, scanner optics or directly in the laser source Deep penetration welding, heat conduction welding or high speed welding Integration for fixed optics, scanner and laser-internal Flexible interfaces: TCP/IP, fieldbus, digital I/O Application examples: e-mobility, battery, body-in-white, seats, gears, airbags, consumer electronics, micro welding |
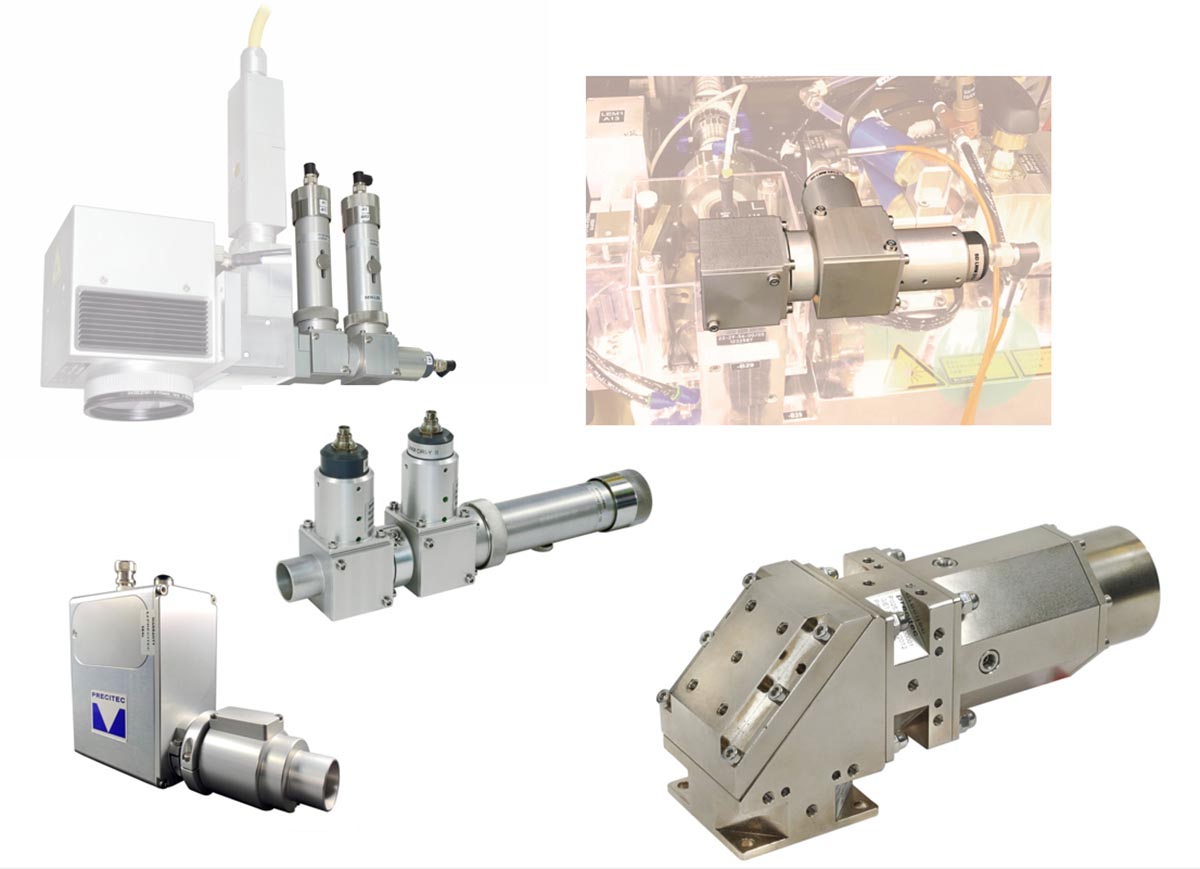