„LASER“, the New Tool for Industrial Cleaning
Lots of researches regarding new technologies for industrial cleaning and surface treatments, has been trying for long time to find new ways to increase productivity and surface quality, or decrease costs. Laser cleaning introduces an efficient and economical alternative to conventional methods. Laser does not require any abrasives or chemicals, which require a special treatment, storing and ecological dispose. Moreover, laser cleaning technology helps to preserve environment by removing abrasives and waste from the cleaning process. All lasers are designed as industrial, almost maintenance-free systems that can be easily integrated into production.
Laser cleaning is certainly state of the art technology, with added value of low costs and quality, as well as scientifically proven long lasting stability. In comparison to the standard technologies, laser cleaning can save up to 90% of operational costs. Furthermore, it has been proven that the return on investment is often less than a year. It is a highly efficient and “green” technology that has gained several environmental awards. Surfaces that has been until now cleaned in several long cycles, laser cleans precisely and contactless during one cycle.
Pre-treatment
Laser cleaning can remove contamination or coating, which usually requires two or more conventional methods to achieve the same result. When laser interacts with the surface (typically metallic), oxide layer is removed, which allows to directly weld metal joints, creating long lasting stability.
In contrary to conventional methods, such as abrasive blasting, solvent or chemical cleaning, laser cleaning has a very unique quality – intact cleaned base material. This quality is especially convenient for surfaces that require constant cleaning during production. Laser technology can be also used as a pre-treatment of contact surfaces for gluing, vaporizing coatings before bonding, partial surface cleaning, etc.
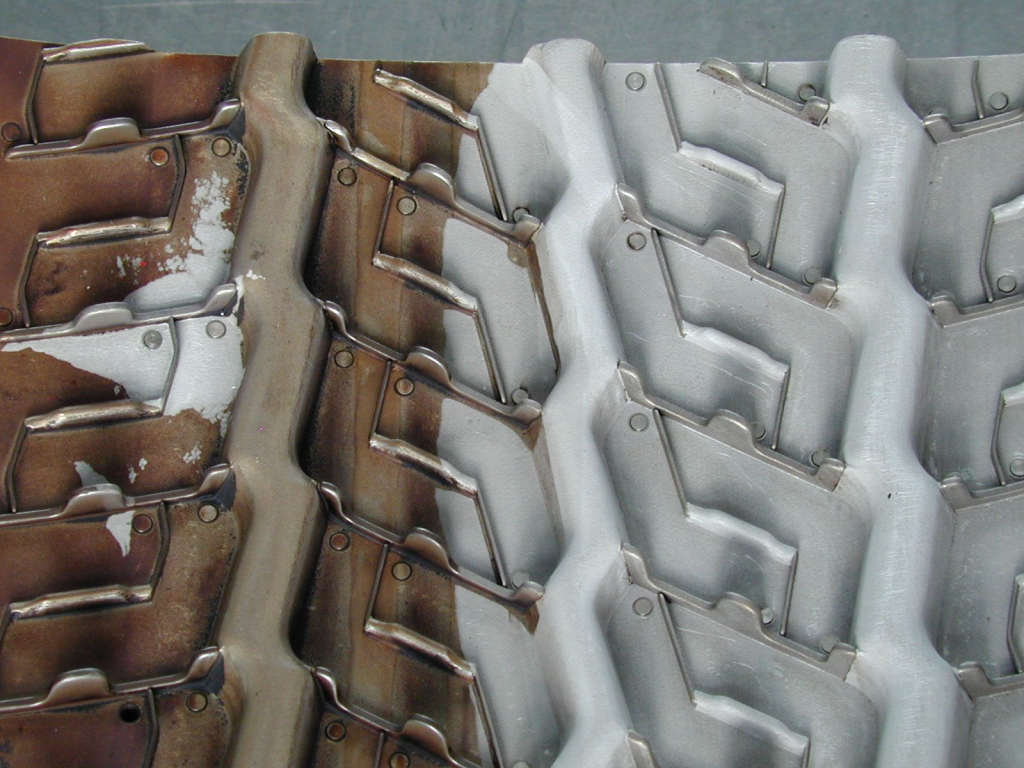
Laser mold cleaning of plastic and rubber surfaces
Local and large-area usage
This technology can be used to clean either large areas or specific portions of a part, both indoors and outdoors. Laser can be complemented by light conducting cable up to 50m to reach areas in height. The exact laser process enables removal of layers in various depths. When the setting is optimized, it is possible to remove only surface coating, preserving deeper layers. This is done so precisely that complex masking becomes redundant. Unlike the fundamental material, layers of impurities, metal and other coatings, absorb the light of laser beam very well. This leads to their heating and subsequent vaporization. The whole process is fast and does not require any complementary abrasive, chemical or mechanical cleaning.
- Laser mold cleaning of plastic and rubber surfaces
- Oxide removal during processes in electronic industry
- Pre-coating surface preparation
- Oil removal from metallic surfaces before welding joints
- Selective de-coating of dioxide layers as preparation for welding
- Finished weld joints care – paint removal
- Structuring and modification of metallic surfaces
- Removal of residues and release agents from plastics as a preparation for subsequent bonding
- Cleaning and pre-treatment for adhesive bonding
- Cleaning and pre-treatment for brazing and welding
- Oil removal in food industry
Do not hesitate to contact us for more information.
Comments are closed.