Lasers for micromachining
Over the recent years, the laser technology and its potentials have been exciting laser manufacturers as well as researchers and industrial users. Lasers with their excellent beam quality promised noticeable advantages and improvements in high precision and material processing at the microscale. The world of laser machining production is divided into micro- and macromachining. This classification is not based on the size of the work piece but rather the fineness of the impact cased by the laser tool. Mechanical engineering uses micromachining especially for drilling small holes (size of 1 um), cutting of ultrathin foils, removing layers, 3D modelling of very small objects or 3D engraving in glass. This technique is not used only for metal but also for glass, polymers, ceramics, carbon or Kevlar composite.
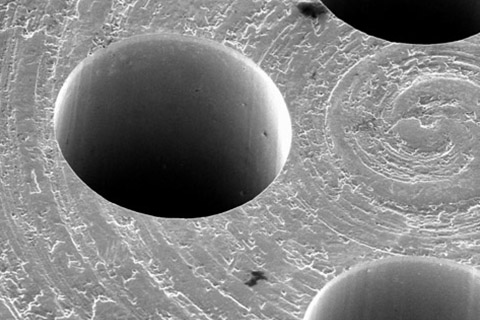
Laser micromachining
The use of extremely short nano- and pico- and even femtosecond pulse durations helps to minimize the thermal effects such as melting and burr formation thus eliminating the need for any post processing measures. Every spot is creating indentiation in scale of um. Networ is not creating only flat but in practise 2.5D structure, changing of focus cause formation of 3D structure. High power density allows to use also lasers with shorter wavelength (335 nm or 532 nm), which is better absorbed in material and allows to use less power.
Surface roughness after the laser micromachining may range up to about 0.3 Ra values, so for most products is no need finishing operations.
Advantage of laser micromachining:
- Easy integration
- Non-contact and fast process
- High accuracy of repeated process
- No need of strong power sources due to shorter wavelengths
- 3D micromachining
- Formation of exact network of spot with low heat affected zone
- Quick investment return
Contact us for more information about laser micromachining.
Comments are closed.