Laser Cleaning Systems
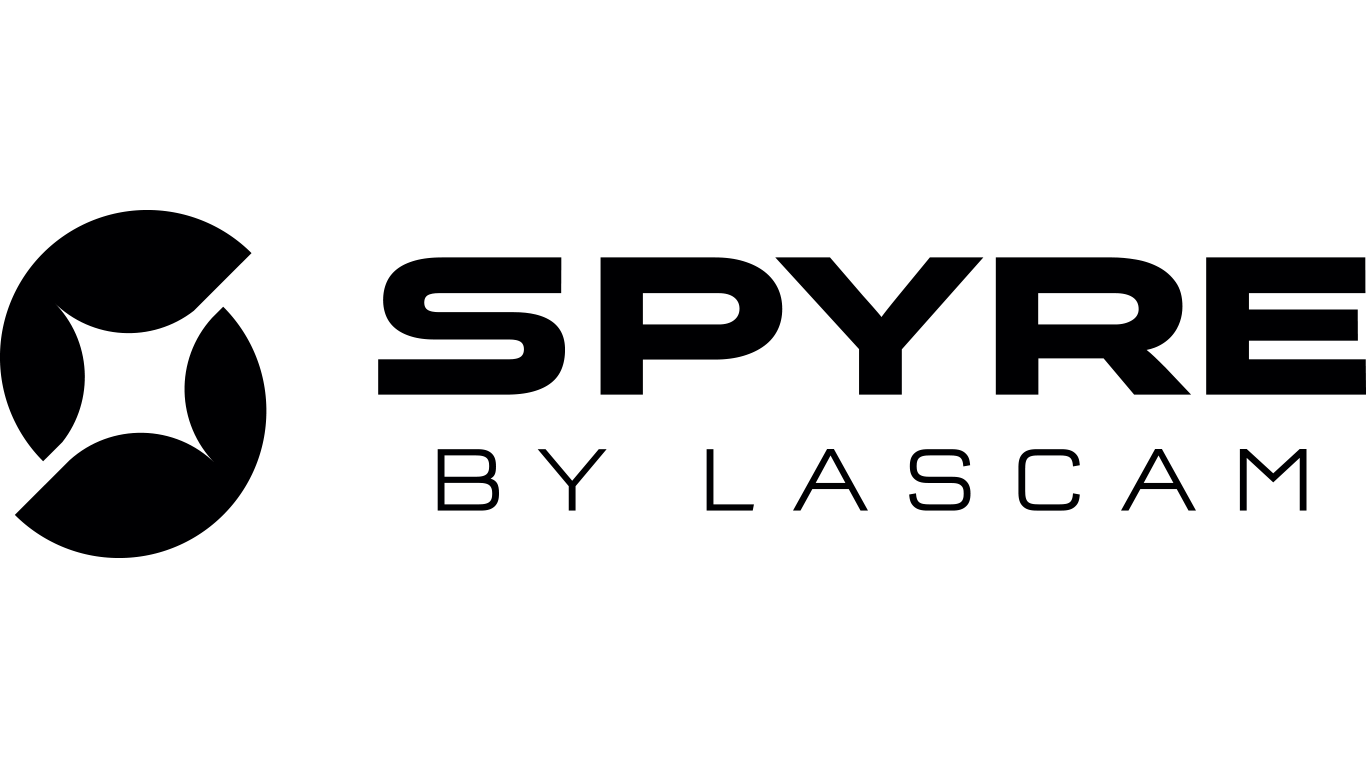
Cleaning lasers and their implementation is one of the key technologies and we have been developing taylor made laser cleaning systems for industrial applications since 2015. We started by selling cleaning lasers from the world’s leading manufacturer and we were among the first to raise awareness about this technology and its implementation in the CEE region, especially in the automotive and plastics industries.
Laser Cleaning
Laser cleaning is an innovative technology that has become an industry standard in recent years, especially in the automotive and aerospace industries. It ensures non-contact removal of dirt, without damaging the surface and heat affecting the base materials. The cleaning technology is highly productive and at the same time certified as green technology with very low operating costs. It does not require any other additives such as chemicals, abrasives, water, etc.
Portfolio
SPYRE cleaning lasers made by LASCAM are designed and manufactured to meet the needs of our customers as well as the highest standards for processing quality and safety. They are suitable for application in continuous production in industry.
Applications
References
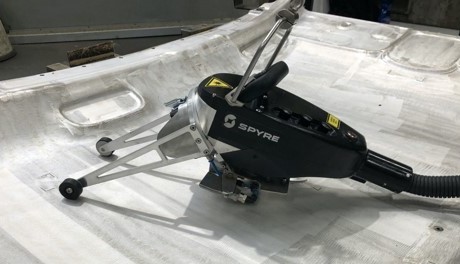
Laser Cleaning of Large Format Molds
Mobile cleaning laser Spyre 500W with a customized attachment for a balancer and a "roller" with castors for easier handling on the mold surface as a replacement for cleaning with chemicals and dry ice. The customer is able to clean 2x more molds per shift with only one operator.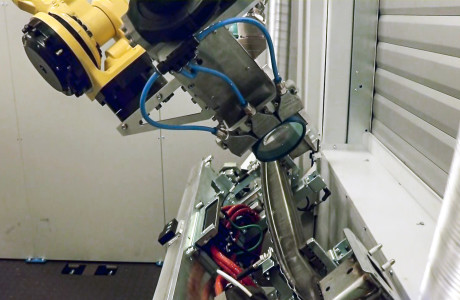
Cleaning of Oil and Operating Impurities before Painting
High-speed cleaning of heating panels embedded in fully automated painting lines. We ensure maximum adhesion of the applied varnish from all sides of the panel. Laser process takes place on the online line and includes a variable assortment size from 500x300 mm to 700x1500.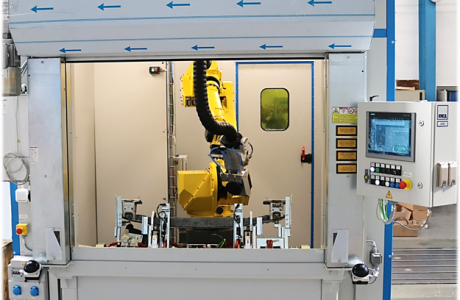
3D Laser Cleaning System C-class 2021 Platform
Automated system made for laser cleaning of welds after SMT and TIG technology before subsequent application of cataphoretic paint. The station is equipped with a 300W fiber pulse cleaning laser with a modified optical path and beam homogenization for removal of silicates, heat, oxides and grease.
Interested in more product information or need service?